Understanding the Cost Dynamics of Pyrolysis Plants
Pyrolysis, the process of breaking down organic materials into smaller molecules in the absence of oxygen, has emerged as a promising technology for converting waste into valuable products such as biofuels, biochar, and syngas. As the world grapples with the challenges of waste management, environmental degradation, and energy security, pyrolysis plants have garnered significant attention for their potential to address these issues simultaneously.
One of the critical considerations for investors, entrepreneurs, and policymakers interested in adopting pyrolysis technology is the pyrolysis plant cost involved in setting up and operating a pyrolysis plant. In this comprehensive guide, we delve into the various factors that influence the cost of pyrolysis plants, from initial investment to ongoing operational expenses.
Understanding Pyrolysis Technology:
Before delving into the cost aspects, it’s essential to understand the basic principles of pyrolysis technology. Pyrolysis involves heating organic materials, such as biomass, plastic, or rubber, in an oxygen-deprived environment, leading to the decomposition of these materials into gases, liquids, and char. These end products can then be further processed into valuable commodities or used as fuels.
The process typically occurs within a reactor vessel, where the feedstock is subjected to high temperatures ranging from 400°C to 800°C, depending on the specific feedstock and desired outputs. Different types of pyrolysis, such as fast pyrolysis, slow pyrolysis, and intermediate pyrolysis, offer distinct advantages and yield different proportions of products.
Factors Influencing Pyrolysis Plant Cost:
Scale and Capacity:
The size and capacity of a pyrolysis plant significantly impact its cost. Larger plants capable of processing higher volumes of feedstock generally entail higher initial investments but may benefit from economies of scale in the long run.
Small-scale pyrolysis units suitable for localized waste management solutions may have lower upfront costs but could be less cost-effective on a per-unit basis.
Technology and Equipment:
The choice of technology and equipment plays a crucial role in determining the cost of a pyrolysis plant. Advanced reactor designs, such as fluidized bed reactors or rotary kilns, may offer higher efficiencies but often come with higher capital costs.
Additionally, the quality and durability of components such as reactors, heating systems, and emissions control equipment influence both upfront and maintenance costs.
Feedstock:
The type and availability of feedstock significantly affect the economics of pyrolysis plants. Biomass feedstocks, such as wood chips, agricultural residues, and energy crops, may be more readily available but could compete with other uses, affecting pricing.
Waste plastics and rubber, while abundant and potentially cheaper, may require additional preprocessing steps to remove contaminants, which can add to operational costs.
Location and Permitting:
The geographical location of a pyrolysis plant can impact its cost due to factors such as land prices, labor costs, and regulatory requirements.
Obtaining permits for waste processing, emissions control, and other environmental regulations may involve regulatory hurdles and associated costs, varying from region to region.
Energy Requirements:
Pyrolysis plants require energy inputs for heating the reactor, maintaining process temperatures, and powering auxiliary systems. The cost of energy, whether from electricity, natural gas, or renewable sources, contributes to operational expenses.
Some batch pyrolysis plants incorporate energy recovery systems to utilize byproducts such as syngas or excess heat, which can offset energy costs over time.
Maintenance and Operating Expenses:
Ongoing maintenance, repair, and replacement of equipment and components constitute a significant portion of the operational expenses for pyrolysis plants.
Labor costs for skilled operators, monitoring and control systems, consumables such as catalysts or sorbents, and waste disposal also contribute to operating expenses.
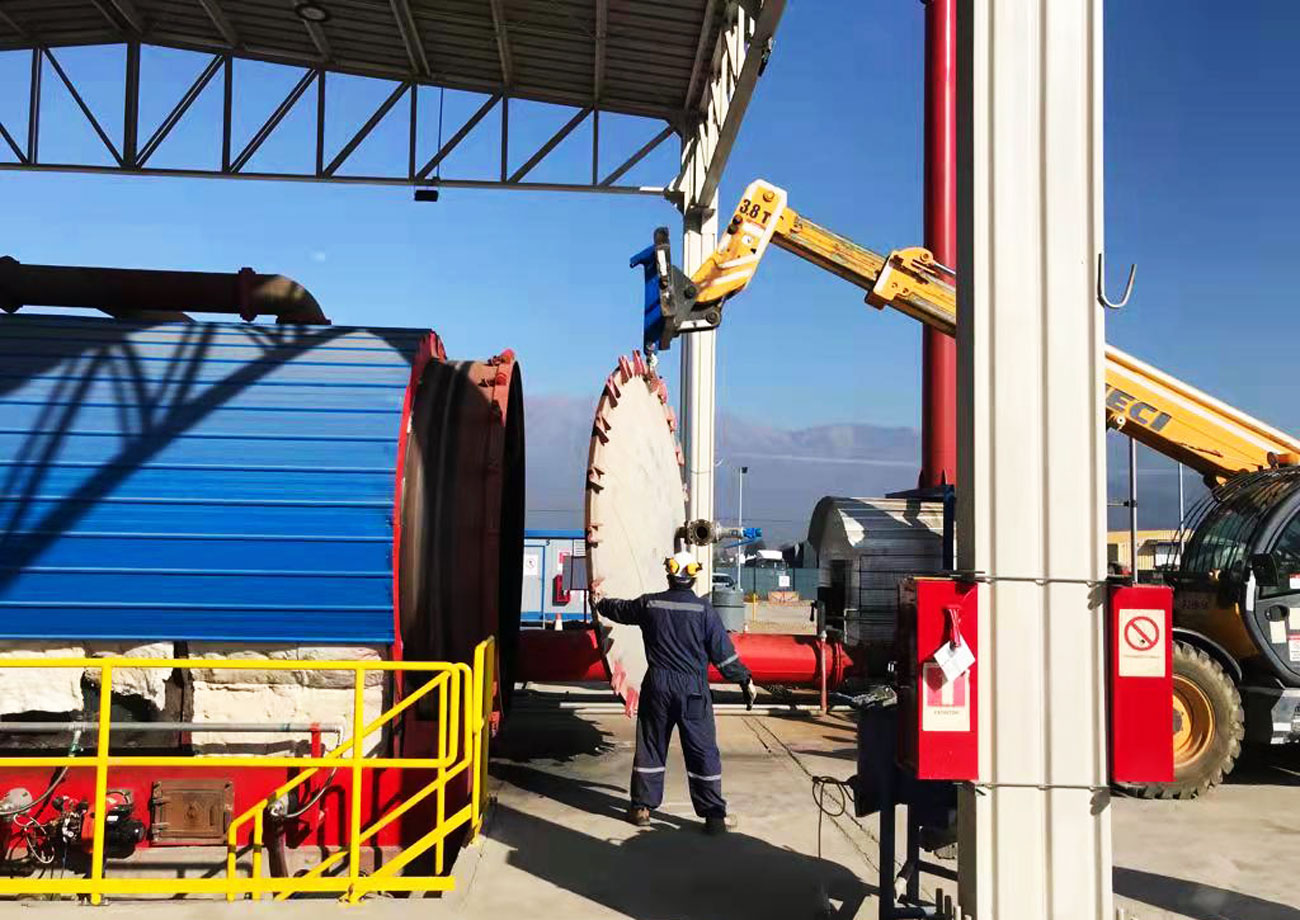
Calculating the Cost of Pyrolysis Plants:
Now that we’ve explored the key factors influencing pyrolysis plant costs, let’s delve into how these factors interact and how investors can estimate the total investment required.
Initial Investment:
The initial investment in a pyrolysis plant encompasses capital expenditures such as land acquisition, construction, equipment procurement, and installation.
Detailed engineering designs and feasibility studies are essential to accurately estimate these costs, accounting for factors such as site preparation, infrastructure requirements, and contingency provisions.
Operating Expenses:
Operating expenses include ongoing costs such as labor, utilities, maintenance, raw materials (feedstock), insurance, and administrative overheads.
Investors should conduct thorough cost analyses to forecast operating expenses over the plant’s expected lifespan, considering factors such as inflation, market fluctuations, and regulatory changes.
Return on Investment (ROI):
Calculating the ROI for a pyrolysis plant involves projecting the revenues generated from the sale of end products (biofuels, biochar, etc.) against the total investment and operating expenses.
Sensitivity analyses, considering various scenarios and assumptions regarding feedstock prices, product markets, and operational efficiencies, can help assess the viability and risk profile of the investment.
Case Studies and Real-World Examples:
To provide concrete insights into the cost dynamics of pyrolysis plants, let’s examine a few real-world examples and case studies:
Example 1: Small-Scale Pyrolysis Plant for Plastic Waste:
Location: Urban area with high plastic waste generation.
Capacity: 1 ton/day.
Technology: Batch pyrolysis reactor.
Investment: $200,000 (inclusive of equipment, permits, and initial operational costs).
Operating Expenses: $50,000 annually (including labor, utilities, maintenance).
ROI: Estimated payback period of 3-4 years based on current market prices for pyrolysis oil and carbon black.
Example 2: Medium-Scale Pyrolysis Plant for Biomass Conversion:
Location: Rural area with access to agricultural residues.
Capacity: 5 tons/day.
Technology: Continuous fast pyrolysis reactor.
Investment: $2 million (including land, equipment, and permitting).
Operating Expenses: $300,000 annually (including feedstock procurement, labor, utilities).
ROI: Expected to break even within 5-6 years, considering revenue from bio-oil sales and potential carbon credit incentives.
Conclusion:
In conclusion, the cost of continuous pyrolysis machine varies significantly depending on factors such as scale, technology, feedstock, location, and regulatory requirements. While the initial investment can be substantial, careful planning, technology selection, and operational optimization are essential for achieving long-term profitability and sustainability.
As the demand for renewable energy, waste management solutions, and circular economy practices continues to grow, pyrolysis technology holds immense potential to contribute to these goals. By understanding the cost dynamics and conducting thorough feasibility analyses, investors and stakeholders can make informed decisions and unlock the benefits of pyrolysis for both the environment and the economy.